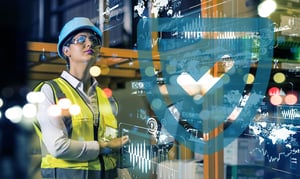
Optimize your Ammonia plant
Optimize your Ammonia plant
Realize up to 3% of efficiency gains through process optimization
Our cloud-based analytics tools and expert insights keep your ammonia plant running at its optimum. Here’s how.
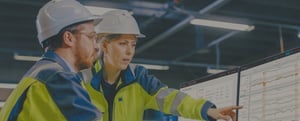
Navigance references in the syngas industry
Navigance is a trusted partner to companies across the global syngas industry, providing ammonia, methanol and hydrogen producers with the tools and insights needed to increase plant efficiency, reduce costs, and enhance sustainability.
Explore Navigance solutions for Ammonia plants
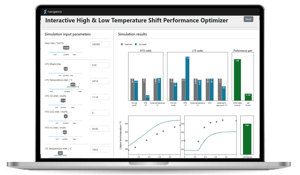
Hybrid process models powered by machine learning for real-time optimization
Read More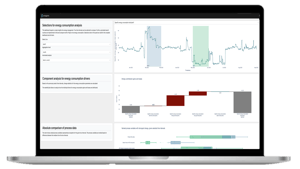
Advanced data analytics to visualize and analyze energy losses and gains
Read More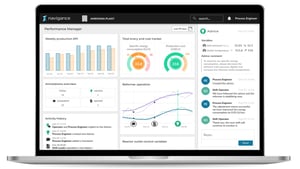
Bridging critical gaps in process monitoring to increase efficiency and stability
Read MoreInteractive Ammonia Optimization
Anticipate the impact of operational changes to steer your process with confidence
The Interactive Optimization tools use cutting-edge machine-learning based models and allow you to:
- Predict the impact of process parameters changes on important KPIs of your plant and take actions proactively and with confidence
- Evaluate different operational scenarios and take smart decisions to keep your plant optimized
Advance the operation of your reformers
Steam reforming or steam methane reforming (SMR) is the predominant technology for the generation of synthesis gas (syngas) via the catalytic conversion of natural gas and/or higher hydrocarbons with steam to produce hydrogen, ammonia and methanol. The performance of the SMR reactor is an important factor in determining the overall efficiency of the process.
Economic impact of steam methane reforming
While in hydrogen production plants steam reforming is responsible for nearly the entire energy consumption, in ammonia production the SMR typically consumes around 50-70% of the total energy, depending on plant design and other factors.
Optimizing the hydrogen production efficiency together with the feed gas and fuel gas consumption is therefore an essential task for the economic operation and for achieving the lowest possible CO2 footprint.
AI-powered models tailored to your plant
The Interactive Reformer Optimization tool is a hybrid process model for primary- and secondary reformers. A pre-configured hybrid neural network for the SMR section is tailored to each plant and trained on historic data.
Plant specific, machine-learning based data analytics are accessible to operators and engineers in an easy-to-use tool on the dashboard. It allows them to predict the impact of changes to process variables such as the plant load, primary reformer outlet temperature, steam to carbon ratio and steam flow to secondary reformer on selected KPIs of the reformers:
- Methane slip at the primary and secondary reformer outlet
- Specific fuel consumption
- Specific feed consumption
Operators and engineers can optimize the operating conditions in the SMR to:
- Minimize fuel and feed consumption
- Predict the performance gain in terms ammonia make and energy savings
Advance the operation of your shift reactors
High temperature shift (HTS) and low temperature shift (LTS) converters play a key role in the economic operation of ammonia and hydrogen plants. Hybrid process models combined with machine learning offer a powerful tool for interactive optimization of these units.
Economic impact of shift reactors
AI-powered models tailored to your plant
The Interactive Shift Optimization tool is a hybrid process model for the HTS and LTS reactors. A preconfigured hybrid neural network for the shift unit is tailored to each plant and trained on historic data.
Optimize your hydrogen make by minimizing CO slip
Operators and engineers can simulate and optimize the operating conditions in the shift reactors based on a plant-specific hybrid process model. An interactive tool enables them to:
- Minimize HTS/LTS reactor CO slip to increase hydrogen gain
- Gain insights into operating conditions relative thermodynamic equilibrium
- Ensure sufficient distance to the dewpoint to protect the LTS catalyst from condensation
- Predict the performance gain in terms of H2 or NH3 make and energy savings
Advance the operation of your CO2 absorber
Paired with the methanation process, the CO2 absorber plays a crucial role in removing CO2 from the process gas before it enters the ammonia synthesis loop. This step is vital for ammonia production, as any residual CO2 in the process gas could compromise the efficiency and longevity of the ammonia synthesis catalyst.
Economic impact of CO2 absorption
CO2 removal from the process gas is an energy-intensive operation that utilizes energy from steam. Achieving lower CO2 slip requires greater energy input. Any residual CO2 in the process gas is converted quantitively in the methanator, consuming hydrogen and thereby reducing the overall process efficiency.
Balancing CO2 removal efficiency with hydrogen consumption in the methanator is critical for both economic operation and minimizing the CO2 footprint of the ammonia plant.
AI-powered models tailored to your plant
The Interactive CO2 Absorber Optimization tool is a hybrid process model for CO2 removal section of your ammonia plant. A pre-configured hybrid neural network for the CO2 absorber and the steam network is tailored to each plant and trained on historic data. Plant specific, machine-learning based data analytics then allow a user to predict the impact of changes to defined process variables on selected KPIs of the CO2 absorber.
Optimize your energy efficiency by optimizing the CO2 slip
Operators and engineers can simulate and optimize the operating conditions in the CO2 absorber section based on a plant-specific hybrid process model. An interactive tool enables them to:
- Optimize the CO2 slip after the absorber to gain hydrogen production efficiency
- Realize energy savings through improved operation
Advance the operation of your ammonia synthesis loop
The ammonia synthesis loop reactor is at the heart of efficient ammonia production, driving high conversion rates of hydrogen and nitrogen to ammonia. Advanced hybrid process models, augmented by machine learning, provide an innovative solution for interactive optimization of this critical unit.
Economic impact of the ammonia synloop
The ammonia synthesis loop is a critical driver of efficiency and profitability in ammonia production, as it determines the final conversion of hydrogen and nitrogen into ammonia. While it consumes less energy compared to upstream units like steam methane reforming, the loop's optimization significantly influences the plant's overall energy efficiency, product yield, and operating costs.
Maximizing ammonia yield and minimizing unconverted gas recycling reduce both energy consumption and operational wear on compressors and turbines. This not only lowers production costs but also improves the plant's CO₂ footprint by reducing the energy required per ton of ammonia produced.
Optimizing the ammonia synthesis loop is thus an essential task for enhancing profitability, minimizing environmental impact, and ensuring the sustainable operation of ammonia plants
AI-powered models tailored to your plant
The Interactive Synloop Optimization tool is a hybrid process model specifically designed for the ammonia synthesis loop reactor. A preconfigured hybrid neural network is customized for each plant and trained on its historical performance data.
Optimize ammonia yield and energy efficiency
Operators and engineers can simulate and optimize the operating conditions in the ammonia synloop using a plant-specific hybrid process model. This interactive tool enables them to:
- Maximize ammonia yield by optimizing reactor conditions
- Improve energy efficiency through fine-tuning of operating parameters
Energy Performance Analyzer
The Energy Performance Analyzer for ammonia plants enables advanced data analytics to visualize and analyze energy losses and gains for defined energy consumption parameters, such as feed gas, fuel gas, steam and electricity consumption.
Discover with ease influencing process variables that effect the energy consumption based on cleaned and relevant operating data:
- Compare selected time periods or benchmark current energy consumption with historic benchmarks
- Visualize energy losses and gains and and deep dive into the influencing process parameters
- Pin-point the top process parameters based on their their change statistics and correlation to energy losses and gains
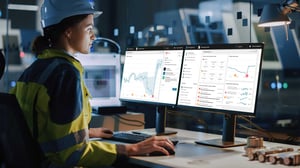
Benefit from advanced energy analytics to take the right actions
Don't waste hours analyzing your process data manually. Compare the specific energy consumption for different times and operational scenarios based on relevant data with just a few clicks.
Gain an understanding of energy losses compared to your plant’s best demonstrated performance.
Discover and investigate the correlations and process conditions that influence energy consumption.
Algorithms analyze the changes of process variables and rank them by their significance for the energy losses and gains.
Take smarter decisions on required actions to adjust process variables settings based on gained insights.
Ammonia Process Soft Sensors
Ammonia production relies on precise control and monitoring of process gas compositions and flows to ensure a safe, reliable and efficient operation of the plant. Traditional hardware sensors, while critical, often face challenges such as high costs, maintenance needs, and limitations in harsh operating conditions. This is where soft sensors - virtual or software-based sensors- bring significant value.
Navigance soft sensors use advanced algorithms, machine learning, and mathematical models to estimate process variables based on existing plant data. By integrating soft sensors into ammonia plants, operators gain a robust and cost-effective tool to complement or replace physical sensors in monitoring gas compositions, flows and process KPIs.
Use cases of soft sensors in the ammonia process:
- Gas composition monitoring: Simulate the reformer or shift reactor outlet gas compositions with soft sensors to gain insights to unit performance.
- Flow rate estimation: Soft sensors for steam or dry gas flows enable their monitoring when physical flowmeters are unavailable or unreliable due to scaling or corrosion.
- Approach-to-Equilibrium (ATE): ATE measures the difference between a reaction’s theoretical maximum conversion and its actual conversion for given operating conditions. For the steam methane reforming and water gas shift reactions, knowing the ATE through a soft sensor is important for optimizing the process conditions to reach best performance.
- Model-based optimization: Process models rely on accurate data to determine optimized operating conditions. Soft sensors can improve data availability where instrumentation is not available or reliable.
- Energy Efficiency Optimization: Soft sensors enable energy savings by identifying inefficiencies in compressors, reformers, and synthesis loops.
Benefits of soft sensors
Soft sensors integrate multiple data sources, such as continuous data from temperature, flow or composition sensors as well as spot measurements and laboratory analysis. Those are combined with models and machine learning to offer consistent and reliable information about the ammonia process operating conditions and performance.
Soft sensors deliver real-time estimates of gas compositions (e.g., hydrogen, nitrogen, and synthesis gas) and flow rates, enabling proactive decision-making and process optimization.
Navigance solutions overview for Ammonia plants
We combine advanced data analytics and the latest AI-based tools in an easy to use web-based interface, so that our customers reach optimal performance of their ammonia plants and improve sustainability.
You can select the right tools and services for your current needs and optimization goals, we provide you with a tailored offer.
Interactive Ammonia Optimization
Tailored models for your optimization targets
Water-gas-shift model (high- and low-temperature shift converter)
CO2 absorber model
Ammonia synthesis loop model
Implementation of a plant specific hybrid process model for defined unit operations, process variables and KPIs your ammonia plant.
The machine learning model will be tailored to plant specifics, including model training with historic data from your plant operation.
We configure the web-based interface according to your needs, including defined operating limits, to allow interactive optimization.
4 - 8 months implementation time
Ammonia Process Soft Sensors
Tailored soft sensors to enhance your process monitoring and optimization
Reformer or shift reactor outlet compositions
Flow rate estimation for steam or dry gas flows
Approach-to-equilibrium (ATE) monitoring
In ammonia plants, soft sensors can estimate critical process variables such as gas compositions, flows and ATE.
They provide accurate and reliable alternatives or complements to physical sensors, which make them invaluable for monitoring performance and optimizing efficiency.
1 - 2 months implementation time
Energy Performance Analyzer
Real-time energy consumption monitoring
Visualization of energy losses and gains
Smart analytics for operational conditions
Benchmarking of best demonstrated plant performance
We configure all variables and calculations for the energy consumption parameters of your ammonia plant, such as fuel gas, process gas, steam and electricity.
A tool in the web-based interface is tailored to your plant and needs. We implement algorithms for analyzing the contributions of process variables to energy gains and losses.
2 - 3 months implementation time
Explore further. Discover more.
Handy tools, useful reads and upcoming events related to our Optimization Engine. Helping you to optimize your chemical process.